Sanierung SIEMENS RUNDFUNK BAUKASTEN (1935)

Hallo,
manchmal hat man Glück, erst klappt es mit dem Siemens Elektro,
kurze Zeit später komme ich zu einem Siemens Rundfunkbaukasten!
Ein paar Teile fehlten, so muß ich nun einiges mehr nachfertigen
bzw. reparieren. Da Federn evtl von allgemeinem Interesse sind,
will ich die Anfertigung der Federn im Siemens-Kasten beschreiben.
Die Federn liegen links und rechts von der oberen gelben Dose
in Jürgens Kastenübersicht (s. o.).
Sie dienen zusammen mit zwei Gewichten (Stücke von Schrauben M10)
als mechanisches Analogon zur Erklärung von Schwingungen, Resonanz
und gekoppelten Kreisen.
Der Federdurchmesser beträgt etwa 9,5 mm, Drahtstärke ist 0,3 mm
und die Länge sind ca 44 Windungen.
Da mir nur ein 1 Meter-Stück eines 0,3 mm Federstahldrahtes zur Verfügung
stand, konnte ich mal mit den Vorversuchen beginnen.
Schraubenfedern wickelt man grundsätzlich auf einen Dorn, der deutlich
kleineren Durchmesser als die fertige Feder haben muß. Den Durchmesser
dieses Dornes galt es zunächst zu ermitteln. Da es (nach meiner Kenntnis)
keine wie auch immer geartete Abschätzung gibt, hilft nur probieren.
Ein Vorversuch mit einem Stück Schraube M6 (hat Wickeldurchmesser
ca. 5 mm) ergab einen Federdurchmesser von 8 mm, ein Dorn von 6 mm
ergab eine Feder von 10,5 mm. Dazwischen liegt also die Wahrheit.
Bevor man einen Dorn auf 5,5 abdreht, kramt man nat. auch nach einer
Fertiglösung, vor allem hätte man gern irgeneine "Kupplung" zu einem
Werkzeuggriff oder Kurbel.
Da war mir das Schicksal gleich wieder wohlgesonnen, in einem schon lange
vergessenen Kästchen fand ich eine Art Kreuzschlitz-Bit mit 5,5 Durchmesser
und einem Sechskant, der in eine 5er Nuß passte.
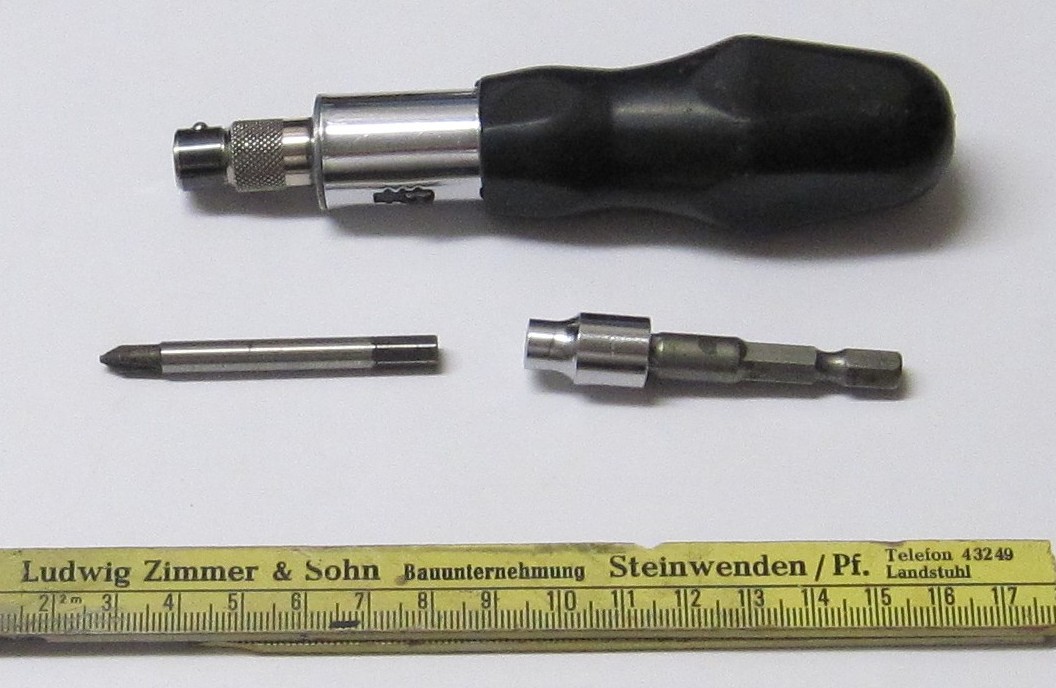
Im Bild der Dorn, mein "Edutec"-Ratschenschlüssel und zwei Stücke eines alten
Zollstocks, der als Bremse und als Auflage für den Wickeldorn dient:
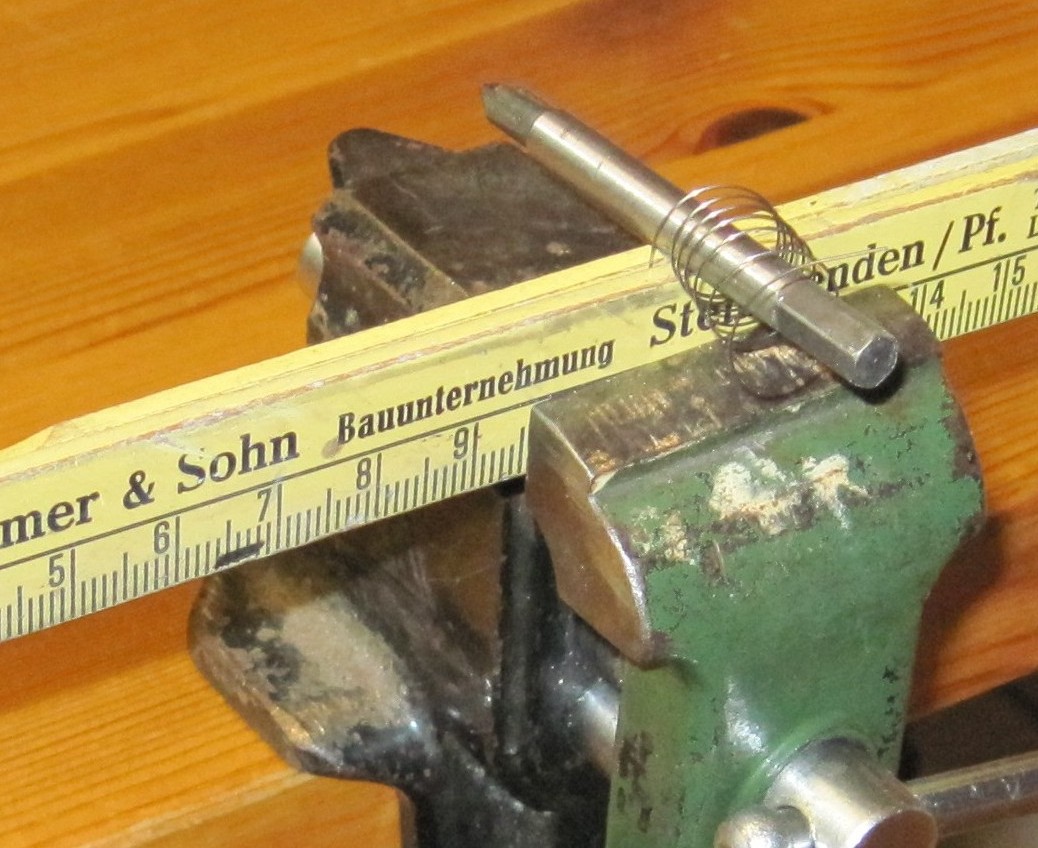
In die beiden Zollstockstücke wurde in die Oberkante eine kleine halbrunde Auskehlung
eingefeilt, und dann wird alles in einen kleinen Schraubstock gespannt.
Der Federstahldraht kommt von unten zwischen den beiden Leistchen hoch, die Spannung
im Schraubstock bremst den Draht so, daß er stramm aufgewickelt wird. Oben im Bild sieht
man nur den Dorn und eine Probefeder(falsch rum gewickelt!), während des Wickelns kann
ich nicht fotografieren :=(
Wird fortgesetzt....
Fortsetzung:
Gestern (12.06) trafen die 10 m 0,3 mm Federstahldraht ein. Schon das Fingergefühl beim
Auspacken sagte mir, daß dieser Draht deutlich "härter" als der Draht ist, mit dem ich
obige Vorversuche anstellte.
Deswegen machte ich zunächst neue Versuche, die zwei Ergebnisse zeitigten:
- längere Federn als ein halb Dutzend Windungen kann man mit der einfachen Bremse
aus den Zollstockhölzchen nicht wickeln. Nach diesen wenigen Windungn hat der Draht
die Hölzchen ausgerieben, die Bremskraft läßt nach. Folge davon ist, daß man Kegelfedern
wickelt, die man gar nicht haben will :=(
- Der neue Draht erfordert tatsächlich einen anderen Dorn.
Aus beiden Umständen ergab sich ein 6-mm Dorn (Schraubenzieher) und ein 5 kg-Gewicht
als Gegenzug beim Aufwickeln.
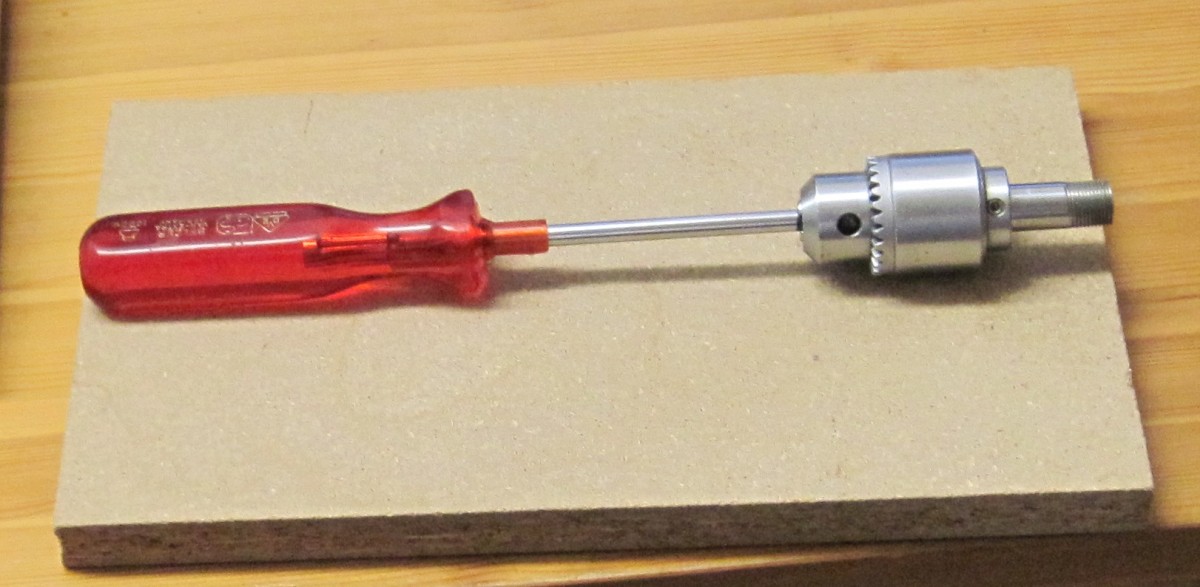
Auf den Kreuzschlitzschraubenzieher ist auf die Spitze ein Rührmotor-Futter aufgesetzt. (rechts)
Dies klemmt den Anfang des Federdrahts fest und ist der zweite Griff beim Drehen.
Da die Schwerkraft recht zuverlässig arbeitet, ist das Gegengewicht eigentlich recht
sympathisch, allerdings beträgt die Drahtlänge rund 1,5 m, man muß also in die
Höhe.
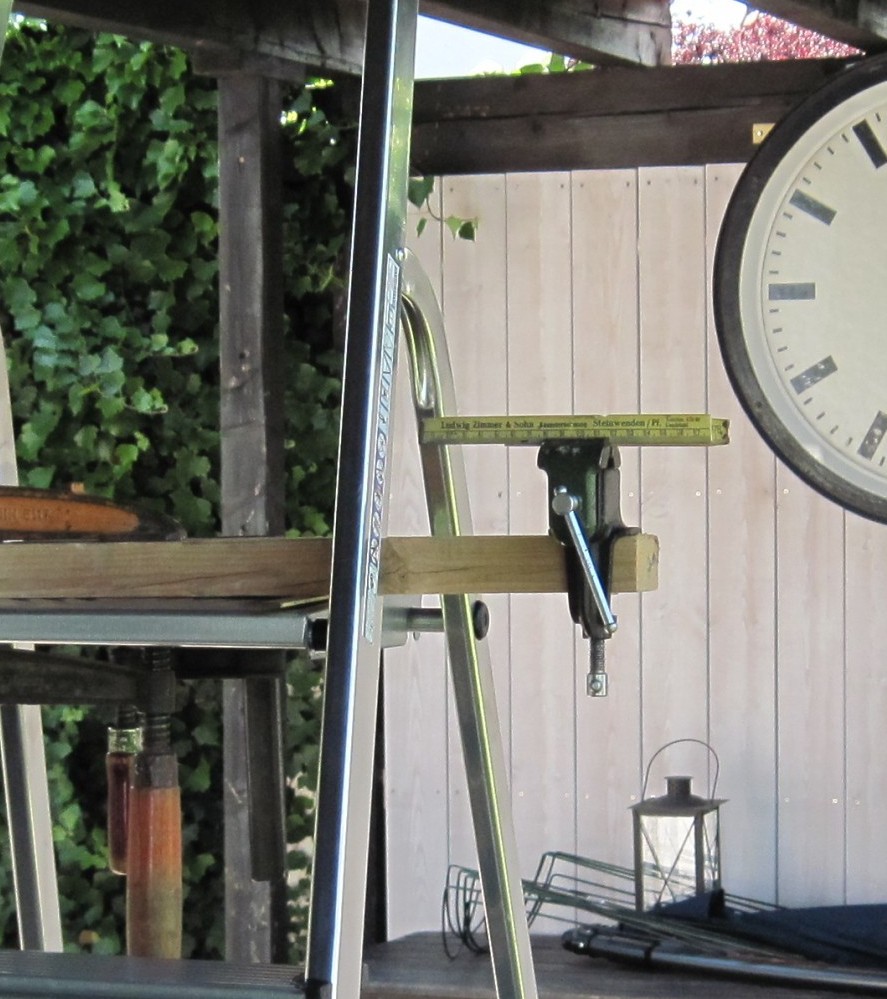
Die Wickelvorrichtung ist auf der Plattform einer Stehleiter montiert.
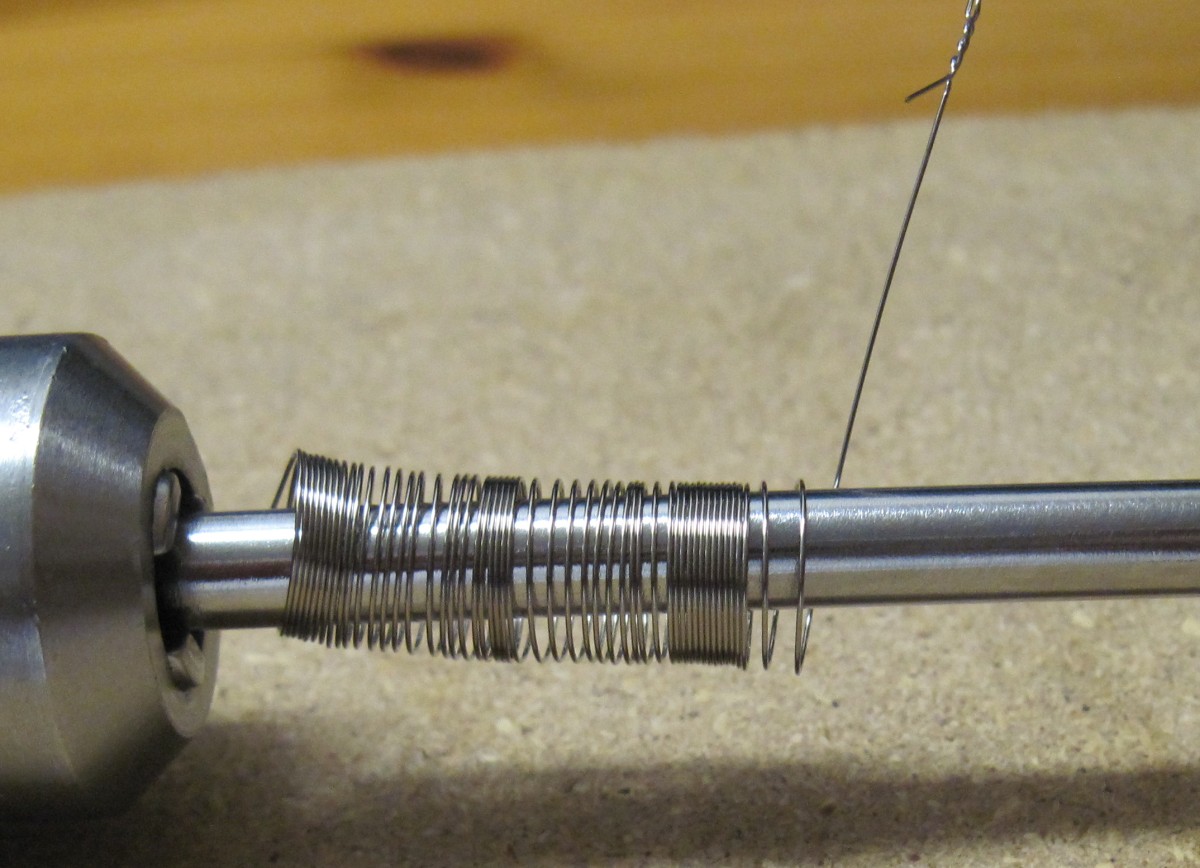
Die erste Feder, noch auf dem Dorn.
In der Steigung kleine Fehler, das habe ich bei den beiden angefertigten
Federn nicht in den Griff bekommen.
Da scheinen mehrere Faktoren mitzuspielen, Vortorsion des Drahts, und
minimale Winkeländerungen beim Drehen des Dorns. Da das aber für
die fertigen Federn in der Anwendung praktisch keine Rolle spielt, habe ich
nicht versucht, es zu korrigieren.
Die erste Feder im Einsatz.
Die zweite Feder war ein Reinfall, ich ließ das Ende mit der Schlinge
unklugerweise einfach los, und sie schnurrte so flott auf, daß sich an
dem Ende einige Windungen unrettbar verhedderten.
Also das Ganze ein drittes Mal. :=(
Generell ist viel "Gäfiehl" angesagt, wenn man ein Drahtende z. B.
zu einer Schlinge rödelt (um das Gewicht einzuhaken). Zu wenig
"rödel" und die Schlinge öffnet sich. Zuviel, und der Draht bricht
bei Belastung.
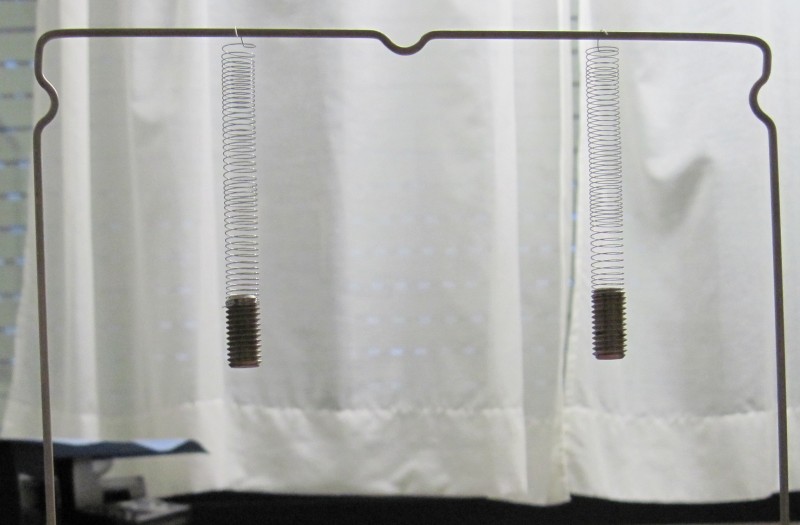
Hier beide Federn nebeneinander mit den Gewichten (Stücke vom Schrauben M10)
Man sieht, daß die Fehler in der Steigung auf die Federkonstante nur gerinegn
Einfluß haben.
Allerdings kann ich nicht sagen, ob die Original-Federn des Kastens
etwa so weich oder hart wie meine waren, ich habe keinen Vergleich.
Für die Versuche ist das nicht von Belang, dafür ist es wichtig,
daß die beiden Federn möglichst übereinstimmen. Eine Feinabstimmung
ist möglich, indem man die Gewichte mehr oder weniger weit einschraubt,
damit wird die jeweilige Feder verkürzt oder verlängert.
Die Länge der Federn mit den Gewichten daran hängend ist etwa 7,5 cm.
Grüße
Georg
manchmal hat man Glück, erst klappt es mit dem Siemens Elektro,
kurze Zeit später komme ich zu einem Siemens Rundfunkbaukasten!
Ein paar Teile fehlten, so muß ich nun einiges mehr nachfertigen
bzw. reparieren. Da Federn evtl von allgemeinem Interesse sind,
will ich die Anfertigung der Federn im Siemens-Kasten beschreiben.
Die Federn liegen links und rechts von der oberen gelben Dose
in Jürgens Kastenübersicht (s. o.).
Sie dienen zusammen mit zwei Gewichten (Stücke von Schrauben M10)
als mechanisches Analogon zur Erklärung von Schwingungen, Resonanz
und gekoppelten Kreisen.
Der Federdurchmesser beträgt etwa 9,5 mm, Drahtstärke ist 0,3 mm
und die Länge sind ca 44 Windungen.
Da mir nur ein 1 Meter-Stück eines 0,3 mm Federstahldrahtes zur Verfügung
stand, konnte ich mal mit den Vorversuchen beginnen.
Schraubenfedern wickelt man grundsätzlich auf einen Dorn, der deutlich
kleineren Durchmesser als die fertige Feder haben muß. Den Durchmesser
dieses Dornes galt es zunächst zu ermitteln. Da es (nach meiner Kenntnis)
keine wie auch immer geartete Abschätzung gibt, hilft nur probieren.
Ein Vorversuch mit einem Stück Schraube M6 (hat Wickeldurchmesser
ca. 5 mm) ergab einen Federdurchmesser von 8 mm, ein Dorn von 6 mm
ergab eine Feder von 10,5 mm. Dazwischen liegt also die Wahrheit.
Bevor man einen Dorn auf 5,5 abdreht, kramt man nat. auch nach einer
Fertiglösung, vor allem hätte man gern irgeneine "Kupplung" zu einem
Werkzeuggriff oder Kurbel.
Da war mir das Schicksal gleich wieder wohlgesonnen, in einem schon lange
vergessenen Kästchen fand ich eine Art Kreuzschlitz-Bit mit 5,5 Durchmesser
und einem Sechskant, der in eine 5er Nuß passte.
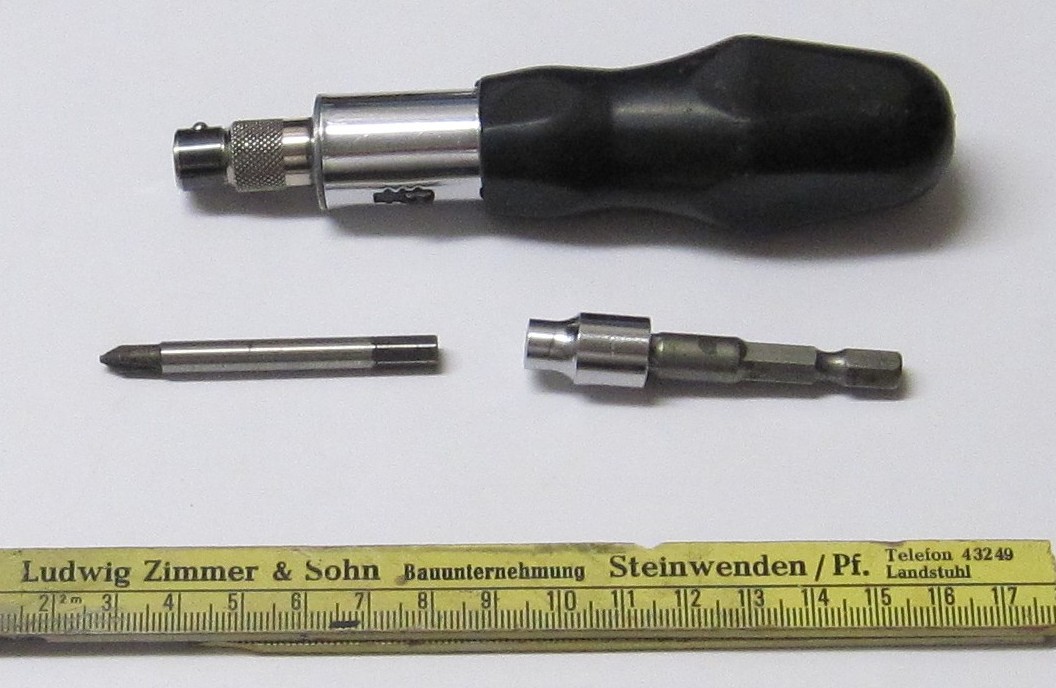
Im Bild der Dorn, mein "Edutec"-Ratschenschlüssel und zwei Stücke eines alten
Zollstocks, der als Bremse und als Auflage für den Wickeldorn dient:
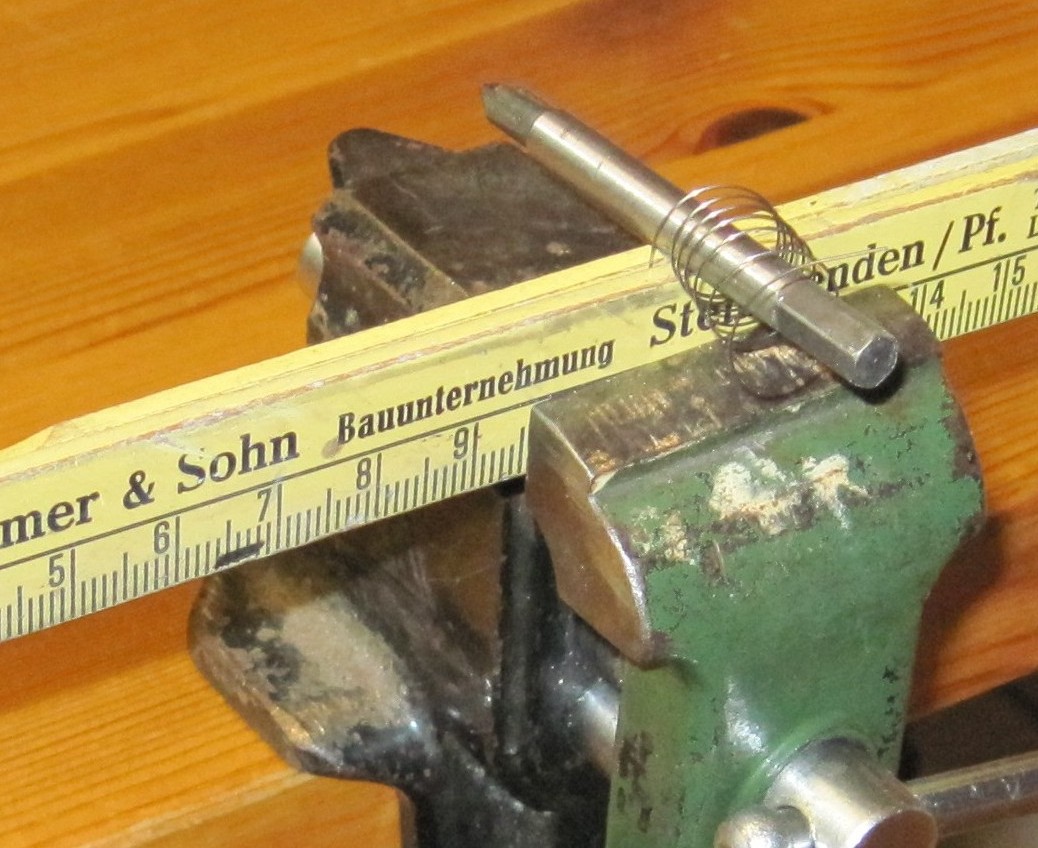
In die beiden Zollstockstücke wurde in die Oberkante eine kleine halbrunde Auskehlung
eingefeilt, und dann wird alles in einen kleinen Schraubstock gespannt.
Der Federstahldraht kommt von unten zwischen den beiden Leistchen hoch, die Spannung
im Schraubstock bremst den Draht so, daß er stramm aufgewickelt wird. Oben im Bild sieht
man nur den Dorn und eine Probefeder(falsch rum gewickelt!), während des Wickelns kann
ich nicht fotografieren :=(
Wird fortgesetzt....
Fortsetzung:
Gestern (12.06) trafen die 10 m 0,3 mm Federstahldraht ein. Schon das Fingergefühl beim
Auspacken sagte mir, daß dieser Draht deutlich "härter" als der Draht ist, mit dem ich
obige Vorversuche anstellte.
Deswegen machte ich zunächst neue Versuche, die zwei Ergebnisse zeitigten:
- längere Federn als ein halb Dutzend Windungen kann man mit der einfachen Bremse
aus den Zollstockhölzchen nicht wickeln. Nach diesen wenigen Windungn hat der Draht
die Hölzchen ausgerieben, die Bremskraft läßt nach. Folge davon ist, daß man Kegelfedern
wickelt, die man gar nicht haben will :=(
- Der neue Draht erfordert tatsächlich einen anderen Dorn.
Aus beiden Umständen ergab sich ein 6-mm Dorn (Schraubenzieher) und ein 5 kg-Gewicht
als Gegenzug beim Aufwickeln.
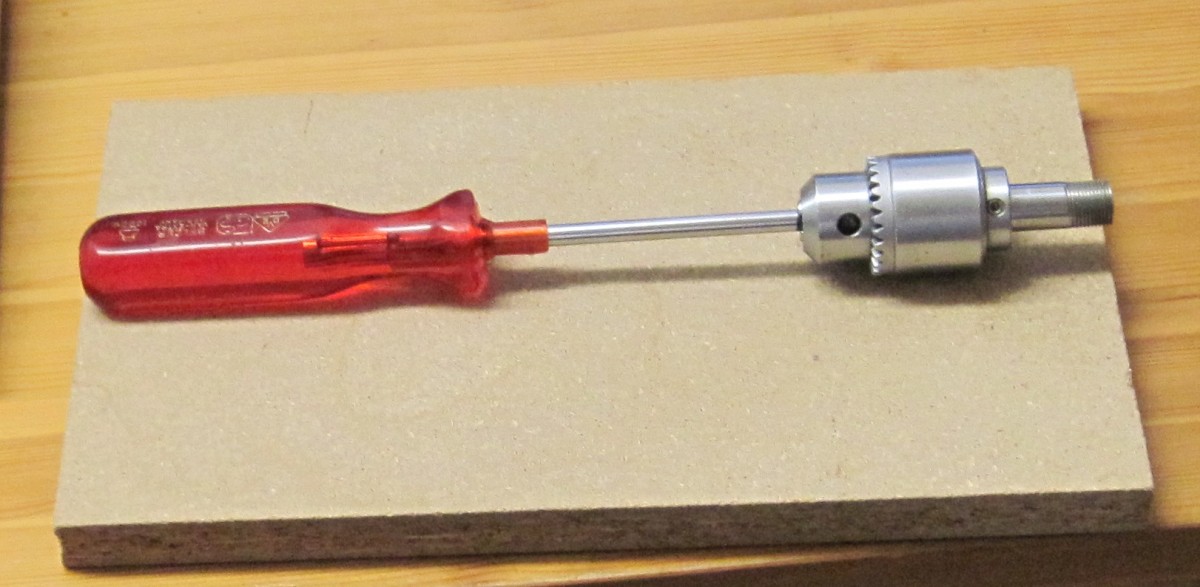
Auf den Kreuzschlitzschraubenzieher ist auf die Spitze ein Rührmotor-Futter aufgesetzt. (rechts)
Dies klemmt den Anfang des Federdrahts fest und ist der zweite Griff beim Drehen.
Da die Schwerkraft recht zuverlässig arbeitet, ist das Gegengewicht eigentlich recht
sympathisch, allerdings beträgt die Drahtlänge rund 1,5 m, man muß also in die
Höhe.
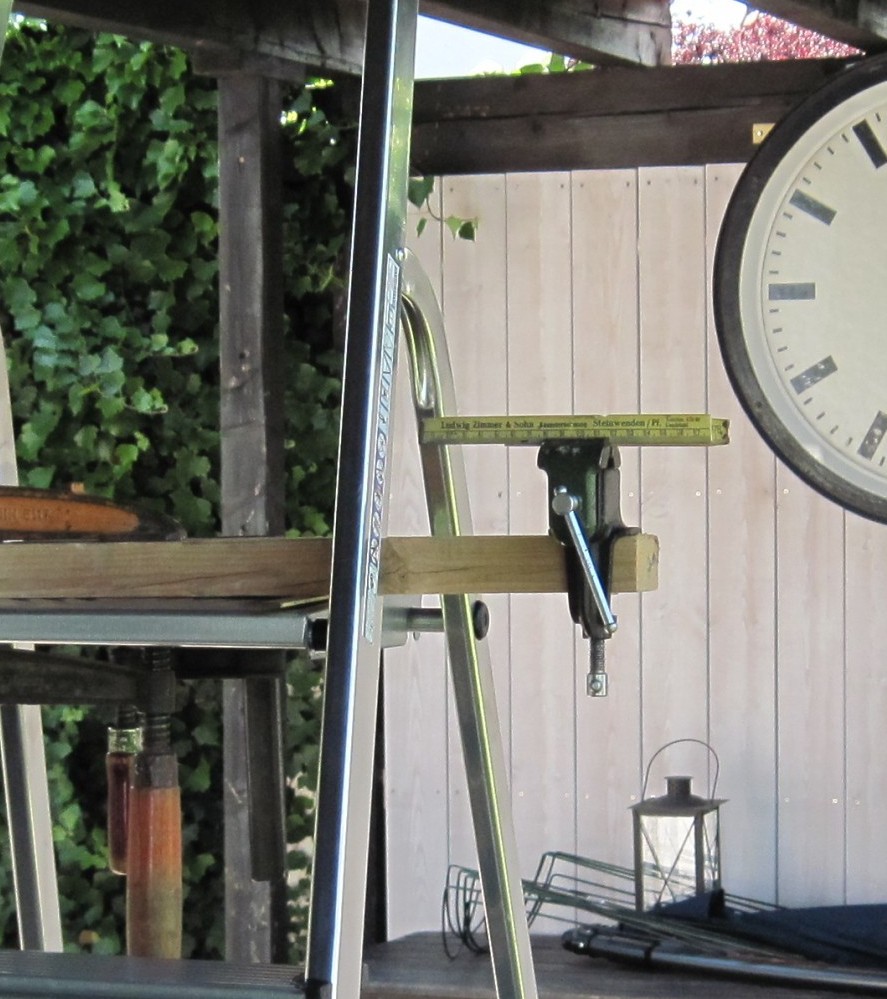
Die Wickelvorrichtung ist auf der Plattform einer Stehleiter montiert.
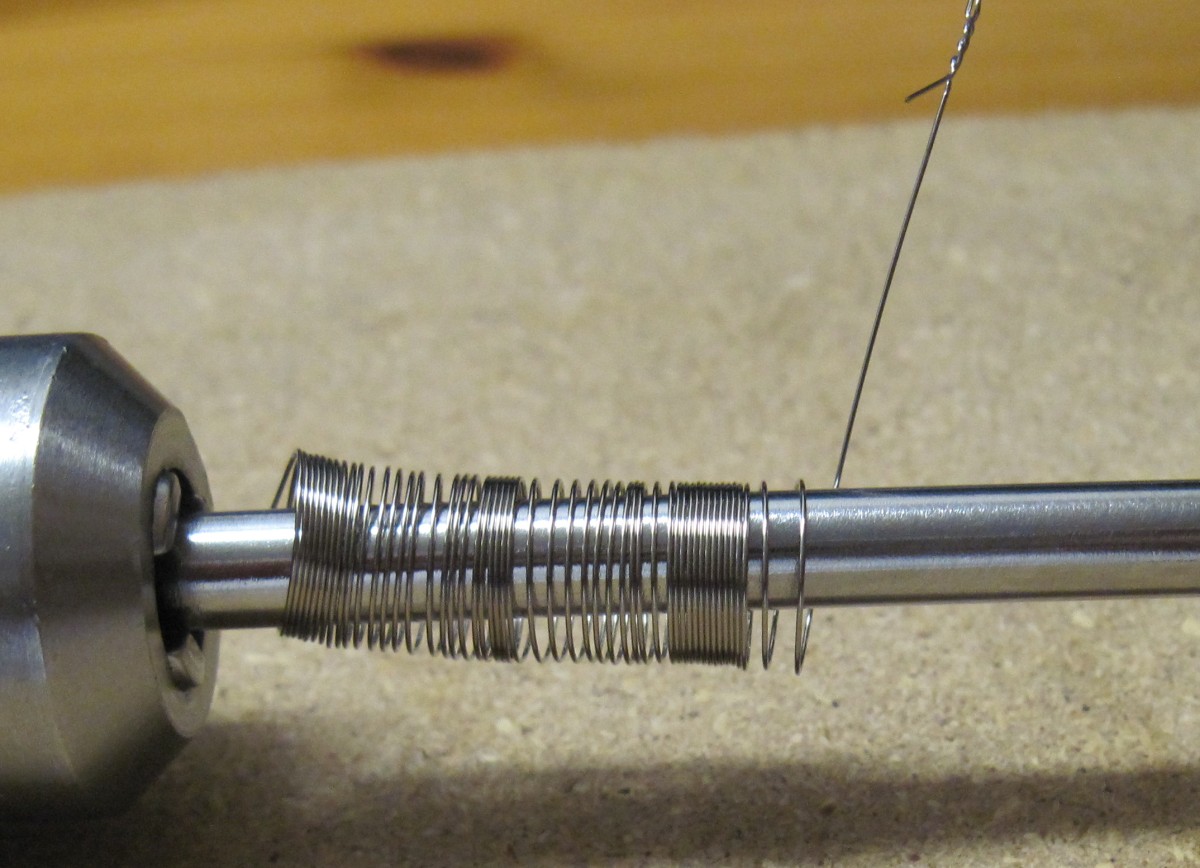
Die erste Feder, noch auf dem Dorn.
In der Steigung kleine Fehler, das habe ich bei den beiden angefertigten
Federn nicht in den Griff bekommen.
Da scheinen mehrere Faktoren mitzuspielen, Vortorsion des Drahts, und
minimale Winkeländerungen beim Drehen des Dorns. Da das aber für
die fertigen Federn in der Anwendung praktisch keine Rolle spielt, habe ich
nicht versucht, es zu korrigieren.
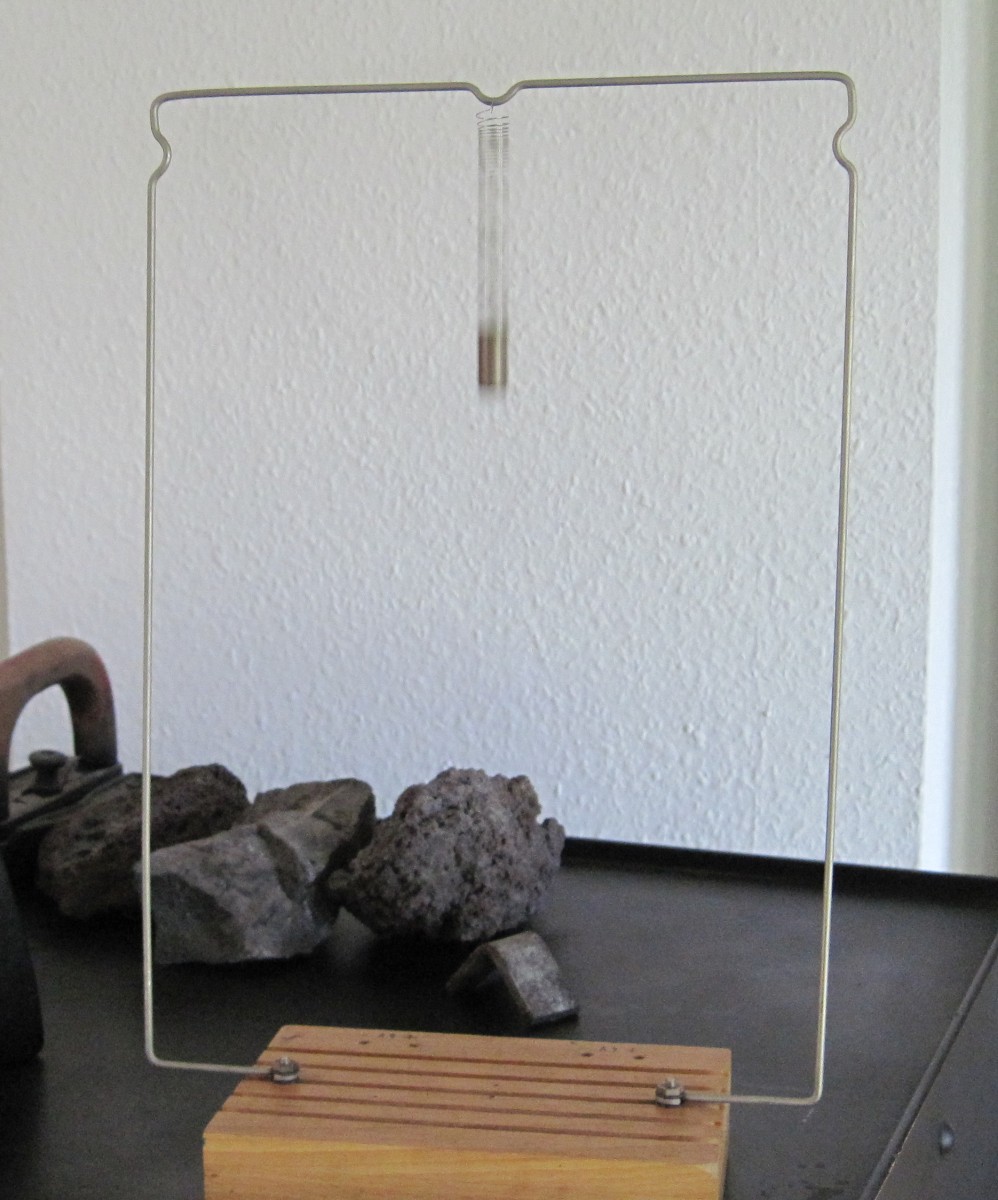
Die erste Feder im Einsatz.
Die zweite Feder war ein Reinfall, ich ließ das Ende mit der Schlinge
unklugerweise einfach los, und sie schnurrte so flott auf, daß sich an
dem Ende einige Windungen unrettbar verhedderten.
Also das Ganze ein drittes Mal. :=(
Generell ist viel "Gäfiehl" angesagt, wenn man ein Drahtende z. B.
zu einer Schlinge rödelt (um das Gewicht einzuhaken). Zu wenig
"rödel" und die Schlinge öffnet sich. Zuviel, und der Draht bricht
bei Belastung.
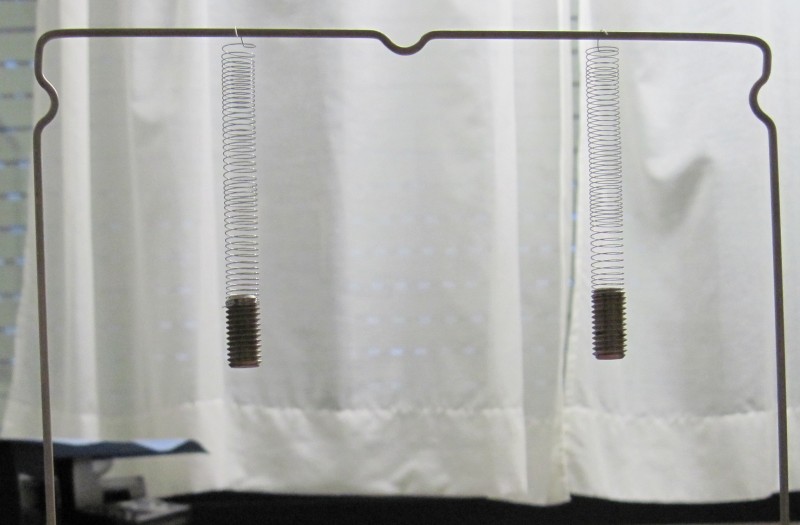
Hier beide Federn nebeneinander mit den Gewichten (Stücke vom Schrauben M10)
Man sieht, daß die Fehler in der Steigung auf die Federkonstante nur gerinegn
Einfluß haben.
Allerdings kann ich nicht sagen, ob die Original-Federn des Kastens
etwa so weich oder hart wie meine waren, ich habe keinen Vergleich.
Für die Versuche ist das nicht von Belang, dafür ist es wichtig,
daß die beiden Federn möglichst übereinstimmen. Eine Feinabstimmung
ist möglich, indem man die Gewichte mehr oder weniger weit einschraubt,
damit wird die jeweilige Feder verkürzt oder verlängert.
Die Länge der Federn mit den Gewichten daran hängend ist etwa 7,5 cm.
Grüße
Georg